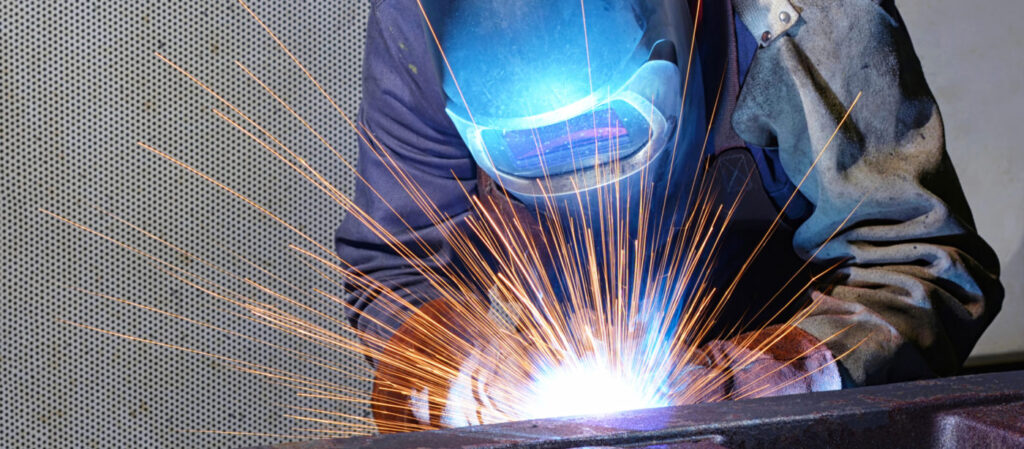
- Fewer replacement parts needed
- Operating efficiency is increased by reducing downtime
- Less expensive base metal can be used
- Helps reduce overall costs
Build-up and Hardfacing
Restoring worn parts frequently involves the following three steps:
1.Buttering : For a deposit that will dilute the carbon and alloy content of the base metal.
2.Build-up : Seriously worn areas should be rebuilt close to working size using tough, crack-resistant welding materials which can be deposited in an unlimited number of layers.
3.Hardfacing : Wear resistant surfaces deposited on the base metal or on built-up deposits extend service life. Hardfacing is usually limited to two to four layers.
Consumable Selection
Base Metal
- Primarily affects the choice of build-up materials.
- Manganese steel is used for components subject to high impact loading. Rebuild to size using manganese steel weld deposits.
- Carbon and alloy steel components are rebuilt to size using low alloy build-up deposits.
- Stainless steel and cast iron base materials may also be addressed for build-up deposits.
Arc Welding Method
The choice of arc welding method depends primarily upon the size and number of the component(s), available positioning equipment and frequency of hardfacing. Available methods are as follows:
- Manual Welding using stick electrodes requires the least amount of equipment and provides maximum flexibility for welding in remote locations and all positions.
- Semiautomatic Welding uses wire feeders and self-shielded or gas-shielded, flux-cored wire increasing deposition rates over manual welding.
Common Hardfacing Considerations
FACTORS TO BE CONSIDERED WHEN SELECTING A SUITABLE WELDING PROCESS
Welding Equipment Type
- What welding equipment is available?
- Is the equipment amperage range adequate for hardfacing?
Process Preference
- Does your equipment or preference lead you to SMAW stick welding, FCAW- semi-automatic welding or SAW mechanized welding?
Consumable Availability
- Do you have required consumables or contact nearest Hardfacing Supplier.
Consumable Diameter
Which SMAW stick or wire diameter is best for your application?
Wire Process Selection
If wire welding, which wire process is best for your application?
FCAW-G Gas-shielded wire, FCAW-S open-arc wire or SAW submerged arc wire?
Operator Skill
What is the level of your operator’s welding skill, process knowledge, hardfacing knowledge?
Welding Location
- Are you welding indoors or outdoors?
- Is there proper and adequate ventilation and/or fume extraction equipment?
Welded Component Configuration
- What is the size, shape and the area to be hardfaced?
Deposit Thickness
- What is the desired deposit thickness or final dimensions?
Deposition Rate
- Do you have specific production targets that determine a target depositon rate?
Welding Position
- Can the component be moved into the flat position for welding or must the weldment be welded out-of-position?
- Are you welding indoors or outdoors?
- Is there proper and adequate ventilation and/or fume extraction equipment?
Welded Component Configuration
What is the size, shape and the area to be hardfaced?
Deposit Thickness
- What is the desired deposit thickness or final dimensions?
Deposition Rate
- Do you have specific production targets that determine a target depositon rate?
- Welding Position • Can the component be moved into the flat position for welding or must the weldment be welded out-of-position?
Machining Requirements
- What are the final surface requirements?
- Is machining required? To what resolution?
Desired Bead Finish
- Will welding beads be left without grinding or machining?
- Will the welds be visible?
- Are there surface finish requirements for appearance?
Component Preparation
- Have the parts been previously hardfaced?
- Is there paint, oil or dirt to be addressed?
Preheat And Post Welding Treatments
- Will the part benefit from specific pre and post heating and cooling practices to achieve maximum hardness, maximum service life or crack resistance?
- What are the final surface requirements?
- Is machining required? To what resolution?
Desired Bead Finish
- Will welding beads be left without grinding or machining?
- Will the welds be visible?
- Are there surface finish requirements for appearance?
Component Preparation
- Have the parts been previously hardfaced?
- Is there paint, oil or dirt to be addressed?
Preheat And Post Welding Treatments
Will the part benefit from specific pre and post heating and cooling practices to achieve maximum hardness, maximum service life or crack resistance?
Applying the Weld Deposits
1. CLEANLINESS
2. SURFACE PREPARATION
3. DEPOSIT THICKNESS
4. PREHEAT AND INTERPASS TEMPERATURE
CAUTION
- Manganese steel becomes brittle if overheated. While a 100°F to 200°F preheat may be required, do not allow interpass temperatures to exceed 500°F.
- Some alloy steel components require a specific heat treatment to perform properly in service. This must be considered when preheating and welding. Contact the part maker for information.
5. DISTORTION
A small amount of distortion can destroy the usability of some parts. Rigid bracing, pre-bending, skip welding and other distortion control techniques may be required.
6. WELDING PROCEDURES
Process Selection
MANUAL ELECTRODE WELDING
Recommended:
Advantages:
1. Highly versatile because it handles:
- Nearly any shape or contour.
- All positions. However, positioning for downhand welding is recommended.
- Small or large parts.
- Any deposit pattern.
2. Inexpensive equipment.
Requires only minimum fixturing and any conventional welder: rectifier or engine driven. DC polarity is recommended, but AC can be used with many electrodes.
Limitations:
1. Labor costs are relatively high because deposition rates are lower than mechanized processes.
2. Human error can result in poor weld quality or a rough surface.
SEMI-AUTOMATIC AND AUTOMATIC WELDING
Recommended:
For large or repeated applications when labor savings offset equipment costs.
Advantages:
1. Low weld costs due to high deposition rates and fast welding speeds can enhance production.
2. Consistent weld quality and a smooth surface are assured by mechanical guidance and automatic controls.
3. Semiautomatic welding with fluxcored wires can typically add greater deposition and an improved bead appearance.
4. Almost any conventional semiautomatic or automatic welder can be used.
Limitations:
- Welding equipment costs can be substantial. Fixturing is also often required.
- Submerged arc welding is limited to the flat position or roundabouts. Its ability to weld contours and odd shapes is limited.
General Guidelines
THE BUILDUP MATERIALS
Some hardfacing deposits have a limited practical deposit thickness. Therefore, rebuild badly worn parts to within 3/16–3/8 in. (4.8mm–9.5mm) of original size before hardfacing. Choice of the buildup material depends primarily on the base metal of the part as follows:
PREPARING THE SURFACE
Remove grease and oil with a solvent and rust and dirt by wire brushing. If not removed, these contaminants can cause porosity, cracking and poor deposit quality. To provide a good bond between base metal and weld, remove cracks, remains of old high alloy.
PREHEAT AND INTERPASS TEMPERATURE
Most applications require preheating, as a minimum to bring the part to room temperature of 70–100°F. Medium to high carbon and low alloy steels may require higher preheat to prevent underbead cracking, weld cracking, spalling, or stress failure of the part.
Higher preheat and interpass temperature are also needed for massive or rigid parts and when cracking actually occurs. Determine the preheat necessary for each job by consulting the Preheat Recommendations table on page 32 of this guide. NEVER OVERHEAT MANGANESE STEEL. KEEP INTERPASS TEMPERATURES BELOW 500°F (260°C). Avoid prolonged and concentrated heat input in any single area. Overheating manganese steel can lead to a brittle condition. Surfacing cast iron parts requires special procedures.
HOW TO APPLY PREHEAT
Preheating is done with gas or oil torches, ovens, or electrical heating devices, depending upon the size of the part and the equipment available. It does no good to heat a part, then let it cool before welding. Always be sure the area to be surfaced is at the specified temperature when starting to weld. Checking the temperature of the part during welding may be needed to be sure it has not cooled. Interpass temperature is the temperature of the surface when welding all layers except the first layer. It is just as important and should usually be as high as the preheat temperature. NEVER OVERHEAT MANGANESE STEEL. KEEP INTERPASS TEMPERATURES BELOW 500°F (260°C).
BUILDUP
Admixture and Cooling Rate
Small beads made with small electrodes and low currents have fast cooling rates and low admixture of base metal into weld metal. Using two layers reduces admixture in the final layer.
PATTERN OF DEPOSIT
Using an appropriate bead pattern can help move more material and extend the equipment life. Here are a few general rules :
- The best pattern is usually the one most economical to apply.
- Since pattern affects shrinkage stresses, it can be used to help control distortion and cracking tendencies.
- A pattern with openings between beads is practical when the openings fill with the abrasive material in service.
- On jobs like crusher rolls, beads placed on the rolls across the flow of material help pull the material through the rolls.
- Beads placed parallel to the flow of abrasive material smooth the flow to reduce wear.
TO OBTAIN THE DESIRED WEAR RESISTANCE, CONTROL ALLOY CONTENT AND COOLING RATE
How to Control Alloy Content
Carbon and alloy content are controlled by both procedures and admixture. Admixture of the electrode metal to the base plate has a very important effect on the wear resistance of the weld deposit. Effective weld metal composition is listed for deposits having the recommended number of weld passes. A single layer of a highly abrasion resistant material, like Chromium Carbide Alloy will not be nearly as abrasion resistant (due to dilution) as a second layer. However, There may be superior alloy can produce high abrasion resistance in the first layer.
How to Control Cooling Rate
Although cooling rate affects wear resistance of some deposits, it is much more important for the control of spalling, cracking and distortion. Therefore, a slow cooling rate may be required even if it reduces wear resistance.
Methods of controlling cooling rate include the following:
- Preheating is the most effective way of slowing the cooling rate.
- Heat input from welding slows cooling by raising the temperature of the part.
Insulating the hot part immediately after welding with dry sand, lime, glass fiber blanket, etc. slows cooling.
This method helps minimize residual cooling stresses, weld cracking and distortion but does not affect wear resistance of most deposits. Remember also, large parts pull heat away from the weld more quickly than small parts. They naturally cool the weld faster.
TO AVOID WELD SPALLING
Prepare the Surface:
As in production welding, hardfacing welds must have a sound crack-free bond with the base metal. Therefore, clean the surface and repair cracks and surface damage.
Avoid Underbead Cracking:
Rapid cooling from welding temperature can cause brittle, crack-sensitive, heat-affected zones in some types of base metal. These zones tend to crack in service causing spalling. To avoid this problem, preheat as specified.
Limit Deposit Thickness
Thick hardfacing deposits build up shrinkage stresses resulting in a greater tendency for spalling. Do not use more hardfacing layers than specified for each type deposit. If thicker deposits are required, utilize more buildup before hardfacing. Peen each layer of thick buildup deposits to relieve stresses.
PREHEAT RECOMMENDATIONS
Low Carbon Steel (to approx. 0.30%C)
- Slightly hardenable.
Preheat 70–300°F (21–149°C). - Preheat heavy parts of over .20%C to 200–300°F (93–149°C). Use the higher temperature for massive, rigid or complex parts.
Medium Carbon Steel (approx. 0.30 to 0.45%C )
- Moderately hardenable, especially in large parts and heavy sections.
- Preheat to 300–500°F (149–260°C). Use the higher temperature for higher carbon contents and for large, rigid or complex parts.
High Carbon Steel (approx. over 0.45%C)
- Highly hardenable and crack sensitive in all sizes and shapes. Preheat to 500–800°F (260–427°C). Use the higher temperatures for the higher carbon contents and for large, rigid or complex shapes
- When carbon content is near .80%, deposit a buttering layer with Excalibur 7018 or a mild steel submerged arc flux and electrode prior to depositing buildup or hardfacing layers. The buttering layer minimizes underbead cracking danger and provides a good bond between base metal and hardfacing deposits.
Low Alloy Steel
- Varies from medium hardenable to highly hardenable depending upon carbon and alloy content. Preheat to 100–500°F (38–260°C). Use the higher temperatures for higher carbon and alloy contents and for large, rigid or complex shapes.
- Preheat temperatures up to 800°F (427°C) or a buttering layer may be required if the carbon content is over .35%C.
Manganese Steel (12-14% Manganese)
- Not hardenable or crack-sensitive. Preheat is not required for thinner sections.
- Preheat massive or highly rigid parts to 100–200°F (38–93°C). Prolonged heating over 500°F (260°C) can cause embrittlement of the manganese steel.
- On small parts, avoid high localized heating by using a skip welding technique.
Cast Iron
Extremely crack sensitive. The heat-affected zone may be full of cracks even with preheat temperatures of 1200–1400°F (650–760°C). Therefore, hardfacing cast iron is often uneconomical. If it must be welded, follow the standard cast iron welding precautions.